The Scientific Research Behind Porosity: A Comprehensive Guide for Welders and Fabricators
Understanding the detailed mechanisms behind porosity in welding is essential for welders and makers aiming for flawless workmanship. From the structure of the base products to the complexities of the welding procedure itself, a plethora of variables conspire to either aggravate or reduce the visibility of porosity.
Understanding Porosity in Welding
FIRST SENTENCE:
Evaluation of porosity in welding reveals essential understandings right into the stability and high quality of the weld joint. Porosity, characterized by the existence of dental caries or gaps within the weld steel, is a typical worry in welding procedures. These voids, if not appropriately attended to, can jeopardize the architectural honesty and mechanical homes of the weld, causing possible failings in the finished item.

To spot and quantify porosity, non-destructive testing methods such as ultrasonic screening or X-ray evaluation are typically employed. These methods enable the identification of interior flaws without jeopardizing the stability of the weld. By examining the size, form, and distribution of porosity within a weld, welders can make informed choices to boost their welding procedures and attain sounder weld joints.
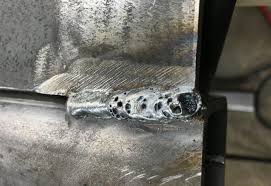
Aspects Affecting Porosity Formation
The occurrence of porosity in welding is affected by a myriad of variables, varying from gas protecting efficiency to the details of welding parameter setups. Welding criteria, consisting of voltage, current, take a trip rate, and electrode kind, additionally influence porosity formation. The welding technique used, such as gas metal arc welding (GMAW) or shielded steel arc welding (SMAW), can affect porosity development due to variations in warm circulation and gas coverage - What is Porosity.
Results of Porosity on Weld High Quality
The visibility of porosity likewise weakens the weld's resistance to rust, as the caught air or gases within the spaces can react with the surrounding environment, leading to deterioration over time. Furthermore, porosity can impede the weld's capacity to hold up against stress or influence, more threatening the overall quality and dependability of the bonded structure. In critical applications such as aerospace, auto, or architectural constructions, where safety and security and durability are extremely important, the detrimental effects of porosity on weld quality can have severe effects, emphasizing the value of lessening porosity via correct welding techniques and procedures.
Strategies to Minimize Porosity
Additionally, using the proper welding criteria, such as the appropriate voltage, existing, and travel speed, is vital in preventing porosity. Keeping a regular arc size and angle throughout welding also aids minimize the possibility of porosity.

Making use of the proper welding strategy, such as back-stepping or employing a weaving motion, can likewise aid distribute warm equally and minimize the chances of porosity formation. By implementing these techniques, welders can effectively reduce porosity and create top notch bonded joints.
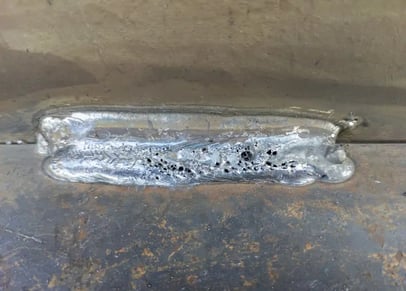
Advanced Solutions for Porosity Control
Implementing innovative technologies and innovative methods plays a crucial duty in achieving exceptional control over find this porosity in welding procedures. One innovative solution is making use of advanced gas blends. Securing gases like helium or a mixture of argon and hydrogen can assist reduce porosity by offering far better arc security and enhanced gas insurance coverage. Additionally, using innovative welding techniques such as pulsed MIG welding or changed ambience her explanation welding can likewise aid mitigate porosity issues.
An additional sophisticated solution entails using advanced welding equipment. Making use of devices with integrated attributes like waveform control and innovative power resources can enhance weld high quality and minimize porosity threats. Moreover, the implementation click reference of automated welding systems with precise control over criteria can dramatically reduce porosity flaws.
Additionally, including sophisticated surveillance and examination modern technologies such as real-time X-ray imaging or automated ultrasonic screening can aid in spotting porosity early in the welding process, enabling immediate corrective actions. In general, integrating these sophisticated remedies can significantly improve porosity control and improve the general high quality of bonded parts.
Verdict
In verdict, recognizing the science behind porosity in welding is vital for welders and fabricators to generate top notch welds. By identifying the factors affecting porosity formation and executing strategies to minimize it, welders can improve the general weld top quality. Advanced solutions for porosity control can better enhance the welding process and make certain a solid and dependable weld. It is vital for welders to continually inform themselves on porosity and carry out best techniques to achieve ideal results.